Manufacturing Process
Wet Milling of PTC Stones
PTC Stones
Manufacturing Equipments
Atomization Equipment
PTC Stones
Manufacturing Equipments
Ceramic Compacting Press
PTC Stones
Manufacturing Equipments
Induction Firing furnace
PTC Stones
Manufacturing Equipments
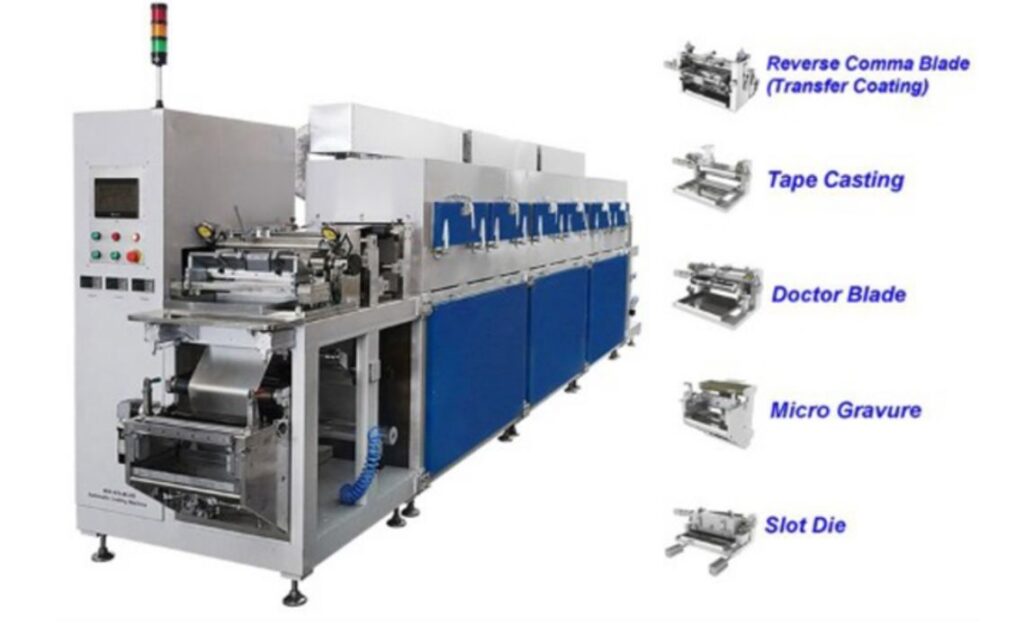
Alumina Substrate
Sheet Manufacturing Equipment
Operation - 1
Thermal Paste Application on Alumina Sheets:
1. One complete set of alumina is placed on to the machine.
2. The placement of alumina could be manual o robotized based on volume
3. The thermal paste dispensing nozzle applies each plate
4. A spatula then spreads the thermal paste evenly on to the alumina surface
Detail Explanation
of Manufacturing Process
Operation - 2
Assembly of Electrode and Ceramic stones:
1. Alumina sheets coupled with thermal paste is brought to operation 2 by robotic arm. Keeping it upside down.
2. Single component Silicon adhesive is applied on to the alumina and in next operation one electrode is placed.
3. A thin layer of single component adhesive again is applied on to the electrode.
4. Required number of PTC ceramic stones are placed on to the electrode by robotic arm.
Detail Explanation
of Manufacturing Process
Operation - 3
Assembly of Electrode and Ceramic stones:
1. Adhesive is again applied on to the top surface of PTC stones.
2. Another electrode is placed on to the top surface of PTC stones.
Detail Explanation
of Manufacturing Process
Operation - 4
Assembly of Alumina Sheet On To The Top Electrode:
1. Alumina sheets coupled with thermal paste is brought to operation 4 by robotic arm. Keeping it such that the Thermal paste surface would be on the top.
2. Now the Heating assembly is ready to be inserted to the tube.
Detail Explanation
of Manufacturing Process
Operation - 5
Placement of Heating Element Inside The Tube
1. Grippers are used to hold the heating element carefully.
2. Grippers lifts the heating element one by one and places it inside the tube.
Detail Explanation
of Manufacturing Process
Operation - 6
Pressing of Tube to arrest heating element inside the tube:
1. A load is applied by hydraulic press the squeeze the tube to arrest heating element inside the tube.
2. No need of putting into the oven as fin is already brazed to the tube top and bottom surfaces.
3. Final check of equivalent resistance is done by quality engineer. If the tube inside surface touches completely to the flat surface of alumina, the measured resistance value should be withing R +/- 5% of calculated value of equivalent resistance.
Detail Explanation
of Manufacturing Process
End of Line Testing Equipment
The End of line test equipment would check followings :
1. Final Resistance value of PTC core
2. Any electrical body leakage
3. Heating of Tube and fin surface when a power supply is given for certain period of time
Operation - 7
Detail Explanation
of Manufacturing Process
PTC Development And
Testing Facilities
High Voltage DC Power Supply
Purpose
1. High power programmable DC power source
2. Model : DCPS 1000 - 12000
Key Features
1. Voltage range : 0 to 1000 V
2. Current range : 0 to 32 A
3. Power range : 0 to 12000 W
4. Dimensions : 423 x 133 x 718 mm ( WxHxD)
5. Display : Graphic display 4.3” Colour touch LCD
6. Front panel controls : Soft keys,Numeric keys, Rotary knob,USB port for transfer and upgrading firmware.
7. Constant voltage (CV), constant current (CC) and constant power (CP) Operation Mode, CC or CV working priority setting
8. Supports master -slave mode, paralleling up to 16 units
Environmental Cycle Test Stand
Purpose
1. Thermal Cycle Environmental Chamber
2. Used to determine the durability of components under changing air temperatures with humidity.
Key Features
1. Temperature -20 to 120 °C with ±1.0°C accuracy
2. 1000mm X 1000mm X 1000mm (W X D X H) 1000ltrs.
3. Controlled Humidity 20% to 97 %
4. Average rate of rise/fall : 2°C/min
5. Heat Dissipation from DUT : Max 6 kw
6. Components are tested to a given number ofcycles or failure
PTC Development And
Testing Facilities
30 Channel Datalogger
Purpose
1. Datalogger
2. Used to monitor and record the temperature, pressure and other sensors with 1 ms sampling speed
Key Features
1. Wireless LAN expandable to 330 channels with plug-in or wireless modules.
2. Monitor data captured remotely on PC with wireless LAN technology.
3. Significantly reduced effects from noise let you safely measure in high voltage and high frequency areas.
4. Expandable in future by adding modules.